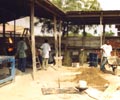
Workshop courtyard
|
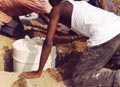
Burying a mould
|
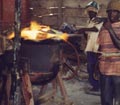
Heating the bronze
|
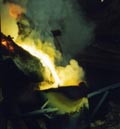
Breathtaking beauty
|
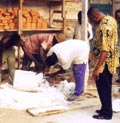
Breaking the mould
|
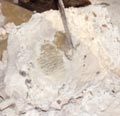
There she is
|
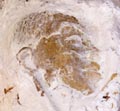
A bit more...
|
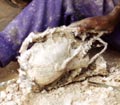
Evacuation chimneys still attached
|
|
For our
joint exhibition at the end of our collaboration Francis made
ceramic pieces, and also bronze and brass figures.
First he
made a basic original in clay. From this he made a two part
plaster mould. He then pressed sheets of wax into the two halves,
and fused the resulting shells together to make a hollow wax
version of his original. Wax details were then added until he
had the model he wanted. This was cast in a plaster mould, which
was placed upside down in his pottery kiln and heated, so that
the wax melts and flows out, leaving a hole inside the plaster
in the shape of his sculpture.
I was at
his workshop glazing some of my work one day when he and his
workers were casting bronzes. He was proud of being the only
Ghanaian sculptor who cast his own bronzes, and rightly so.
He is full
of ingenious ideas for how to find a way round the problems
of doing it under local conditions. The raw material for the
bronze came from the boat scrap yard at Tema docks. Broken boat
propellers, marine fittings, and anything else in bronze, brass
& copper can be put aside for him. The copper wire I used for
the legs and necks of my birds was sections of heavy duty electrical
cable that came from the same source (it took a few of us a
while to strip, untwist and straighten the wires). The wax he
uses for the moulds is beeswax, as it resists the local temperature.
His plaster moulds, cast inside adjustable size sections of
oil drum, are full of bits of broken pottery. This helps the
mould to not split when the molten bronze is poured into it
at very high temperature. Because of the risk of the moulds
splitting they dug holes in the dirt courtyard of his workshop
compound, and the moulds were semi buried in these holes to
hold them firm. If a mould splits there is only a fine sliver
of bronze that escapes into the crack - which can easily be
removed afterwards. After cooling for a while the moulds were
dug out. They were still hot, so one way of lifting them out
of the hole is to protect yourself from the heat by putting
an old pair of jeans on your arms as "gloves". The moulds were
then broken open to reveal the bronze figure, which was covered
in remnants of the plaster. The piece then had to be trimmed,
cleaned, and polished.
Well
done Francis.
|
|